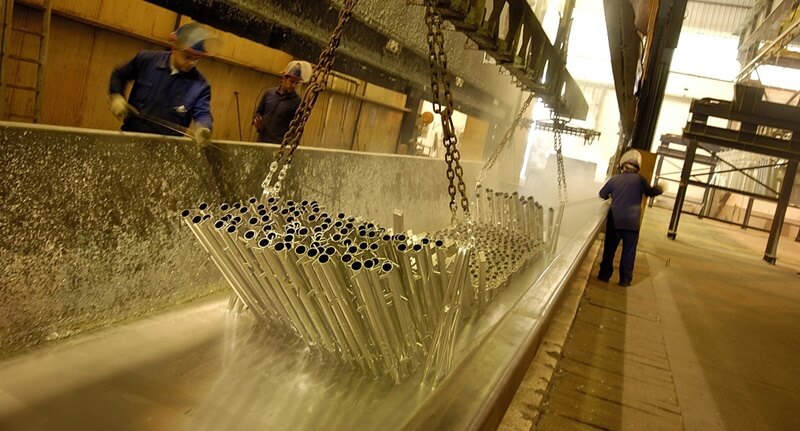
- Feb 15, 2019
- Aldair Teutle
- Uncategorized
- 0 Comments
El proceso de galvanizado consta de diversas fases que hacen posible lograr la aleación. Como se ha mencionado en el artículo sobre las ventajas del acero galvanizado, existen diversos métodos de conseguirla. Cada uno de ellos ofrece resultados distintos.
El propósito de fabricar una aleación es mejorar las características y propiedades de un metal. Y de esta forma tener nuevas funcionalidades.
Principalmente, lo que se busca es aumentar la resistencia y durabilidad del producto, extendiendo su vida útil. Recuerda que la galvanización es dotar al acero o al hierro de una capa de zinc para protegerlos. Te menciono a estos dos metales por ser los más usuales de galvanizar.
Dicha capa se funde y se genera una unión metalurgia sólida y duradera. De las diversas técnicas para efectuar esta aleación, las más importantes son el galvanizado por inmersión y el galvanizado electrolítico.
Proceso de galvanizado por inmersión
En esta entrada, el proceso a abordar es el de inmersión en caliente por ser el más común. Este proceso consta de dos modalidades: a partir de bobinas de chapa y el hecho en cubas.
La diferencia entre las dos es el espesor del acero. El primero se enfoca en grosores no elevados y el segundo en espesores gruesos. Para ambas el procedimiento es similar y no hay cambios sustanciales.
Etapas de galvanizado por inmersión en caliente
Antes de dar comienzo al procedimiento, cada pieza a galvanizar llamada bobina de chapa, se debe examinar visualmente. Dichas piezas deben cumplir con ciertas dimensiones para poder ser sumergidas en el baño de crisol.
Asimismo, las piezas deben poseer una forma geométrica “amigable” o adecuada para permitir escurrir el zinc fundido excedente. De esta forma no se van a formar depósitos y el zincado es uniforme.
Una vez que finaliza la inspección, se procede a colgar las piezas para dar paso al desarrollo del galvanizado. El proceso consta de las siguientes etapas:
- Desengrase o limpieza cáustica: Se remueven toda clase de residuos de la superficie. como pueden ser grasas, aceites, pintura, etcétera.
- Enjuague: Se realiza la limpieza con agua para dejar la superficie lista.
- Decapado: Mediante la aplicación de soluciones de ácido clorhídrico se eliminan impurezas en el material, como puede ser el óxido.
- Segundo enjuague: Se remueven residuos y la solución ácida.
- Solución de Flux: Se aplica esta solución fundente, con el objetivo de recubrir el material a galvanizar con el objetivo de activar la superficie y facilitar la reacción química con el zinc.
- Baño de zinc, “zincado” o simplemente galvanizado: Se sumergen las piezas a una temperatura que puede alcanzar los 460 grados. El tiempo sumergidos depende del espesor, composición del acero y la temperatura del baño de zinc. Generalmente, el producto debe permanecer sumergido hasta alcanzar la temperatura del baño.
- Enfriamiento y limpieza: Finalmente, se enfría el material mediante agua o al aire. Se expelen rebabas y otros restos que se adhieren a la superficie.
Como último paso figura la inspección para el control de calidad. Se lleva a cabo con equipos magnéticos para medir espesores y también de forma visual para evaluar el acabado.
En caso de encontrar anomalías, o de no cumplir con los requerimientos de un cliente en concreto, se toman medidas correctivas. Éstas incluyen una regalvanización total o parcial.
Una vez todo aprobado, el producto final está listo para la entrega al cliente.
Recuerda que en ThermoPanel® somos expertos en paneles de acero galvanizado. Nuestras láminas de acero están recubiertas de una aleación compuesta por aluminio, zinc y silicio mediante un proceso continuo de inmersión térmica. Esta composición ofrece mayores propiedades. Si deseas contactarnos estamos para atenderte.